Operating from the Griffin Industrial Estate in Rowley Regis on the edge of Birmingham and in the very heart of the industrial West Midlands. We provide a local collection and delivery service to our customers, ensuring the highest standard of service and convenience.
Birmingham Garage & Industrial Doors Limited commissioned an RDM, state of the art, continuous process powder coating plant, with a Vixen 4 stage pre-treatment plant. This latter plant is particularly used where aluminium products require effective and thorough cleaning and phosphating prior to powder coating.
For larger and more cumbersome components and products, BGID offer a 3000mm. Waterwash spray booth, which is matched to a 3000 mm. x 2000 mm. Box Oven.
Birmingham Garage & Industrial Doors Limited has rigs for small components, or can accommodate materials up to 7.5 metres long – short runs or larger quantities are welcome. We can undertake straight forward sub assembly and finishing operations where required, thus reducing handling costs and lead times.
With over 180, colours and shades from the RAL standard range in stock, varying from Matt, or Semi-Gloss through to Gloss and some shades also in Textured finish, we can offer fast availability.
Need help? Ask a question
Repairs and Servicing Number: 0121 559 8666
Out of Hours Emergency 24/7 Callout: 07778 375 310
Or send us message below
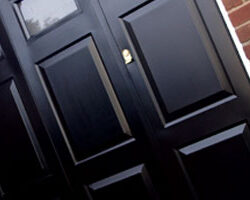
Garage Doors
BGID manufacture, supply and install our own Rowley Range steel side hinged garage doors – these doors are of outstanding specification and construction and are all purpose-made to suit individual opening and client requirements. We also supply and install Garador Up & Overs and Sectionals, as well as Aluroll Roller Shutters.
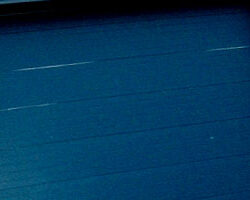
Industrial Doors
BGID has been manufacturing, supplying, and installing industrial doors and roller shutters for the commercial and security sectors, for 50 years.
The Company has earned an enviable reputation for its experience, expertise and customer service in the area
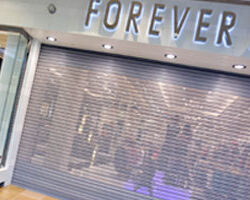
Securi-Store
From a local convenience store to large supermarkets, the Securi-Store range provides a visible, physical security system. Full shop front systems; curtain walling, roller shutters, window grilles, and bars as well as a range of complementary products; door and frame sets, security boxes, cupboards, and much more
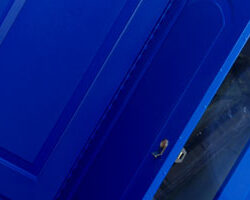
Powder-Coating
Our powder coating facility offers fast, flexible and quality finishes to your steel products with 180 RAL colours to choose from.
We also offer steel fabrication services to create bespoke gates and barriers, security cupboards and doors manufactured and powder coated in-house at BGID
Find us
Birmingham Garage and
Industrial Doors Ltd
Units 3, 10, 12
Griffin Industrial Estate
Penncricket Lane
Birmingham
B65 0SN
© Birmingham Garage & Industrial Doors Ltd. 2022. All Rights Reserved. | Design by Quras Digital